Many EV professionals would argue that Planned Value is one of the most important metrics in earned value analysis. It provides the critical benchmark from which numerous other metrics are being compared.
To give you an idea of what PV is, consider the example where you have a $1 million project that is scheduled to take 10 months to complete. An important aspect of project controls is to be able to plan out how that $1m will be spent over the 10 months. It obviously won’t be spent in one single lump. Neither will it be spent in an even, perfectly distributed rate over the 10 months.
The project spend will follow an uneven pattern – loosely following the schedule of activities and purchases that occur over the project’s duration. Planning the budget over the project’s timeline is called Time-Phased Budgeting. Planned Value is the value of scheduled project spend at a point in time of a project’s duration.
Planned value is also referred to as Budgeted Cost of Work Scheduled (BCWS).
The role of PV is significant in this analysis since, without it, EV and AC are practically meaningless. If they can’t be compared against what was planned, they’re just numbers.
SPI also uses planned value in its calculation. SPI is a key performance indicator that shows how efficiently time is being utilized on a project. A value of greater than 1 means that your project is running better than planned efficiency – and a value less than 1 means less than planned efficiency.
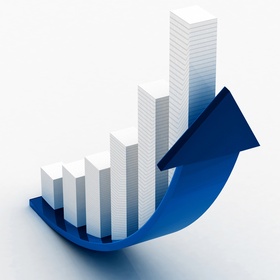
Comparing Planned Value against Earned Value and Actual Cost
Calculating Planned Value is dependent on there being a time-phased budget in place for the project. By time-phasing the budget, project controls can determine what the expected budget outlay is planned to be at any point during the project. Once the project has been underway for two months for example, a PV calculation will tell you how much of that budget was supposed to have been spent by that point in time. The answer, as I’m sure you’ve guessed, is not 20% of that 10-month project. The calculation has to take into account every item or activity budgeted on the project; and determine when exactly the cost is expected to be incurred for that item or activity, based on its scheduled time of completion or delivery. Calculating PV therefore, requires a complex algorithm based on what, when and how much for the entire project. We’ll talk about the details of the calculation further down – what’s important to understand, is that this calculation can determine PV to a precision of a day. In other words, I can pick any date on the calendar and the system will return PV for that day (as long as the date is within the schedule of the project). This is key because PV is being used to compare against Actual Cost and Earned Value to get a picture of the project’s performance and health. In order to obtain an accurate and relevant comparison of these three metrics, they all have to be aligned to a single day. These three metrics tell us the following:- Planned Value: The progress that was planned to be completed by this date
- Earned Value: The actual progress that has been completed at this date
- Actual Cost: The costs that have been incurred to this date
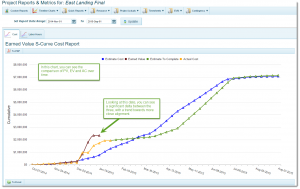
Baseline versus Adjusted PV
Planned Value is of course subject to change over the course of a project’s life. This is a result of scope changes, schedule changes and unplanned productivity issues that result in change orders added to the project. PV for any status date therefore, will adjust according to any approved budget and schedule changes that have occurred on the project. It’s important however, to ensure that the baseline budget and schedule have been locked and are available as a reference point so that project controls can clearly see the delta between what was originally planned (baseline) and what is currently planned. Click on the chart to the right to see an example of Baseline compared to the Current, or adjusted, budget and how they play out over time. The red popup displays when you hover your mouse over any of the status points on any of the lines. The Pending, Actual and Forecast lines have been deliberately turned off for this example, but they are also critical for this type of comparative analysis.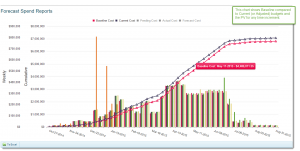
Schedule Variance and Schedule Performance Indicator (SPI)
Planned value is also used in the calculation of both SV and SPI. As mentioned above, Planned Value relates to the schedule in that budget items & activities are time-phased. Calculating schedule variance is done by simply subtracting Planned Value from Earned Value:
Schedule Variance (SV) = Earned Value (EV) − Planned Value (PV)
This formula is saying, “Take the value of the progress completed to date, and subtract what was planned to have been completed, and that’s the variance in schedule.” A negative SV means you’ve completed less than expected by this point, so you’re behind schedule. Most project managers like to see SV in the form of a percent:
SV % = Schedule Variance (SV) ⁄ Planned Value (PV)
SPI = Earned Value (EV) ⁄ Planned Value (PV)